
Case Study
Subsea Global Solutions Straightens Damaged Propeller Blades in a Single 12-Hour Shift
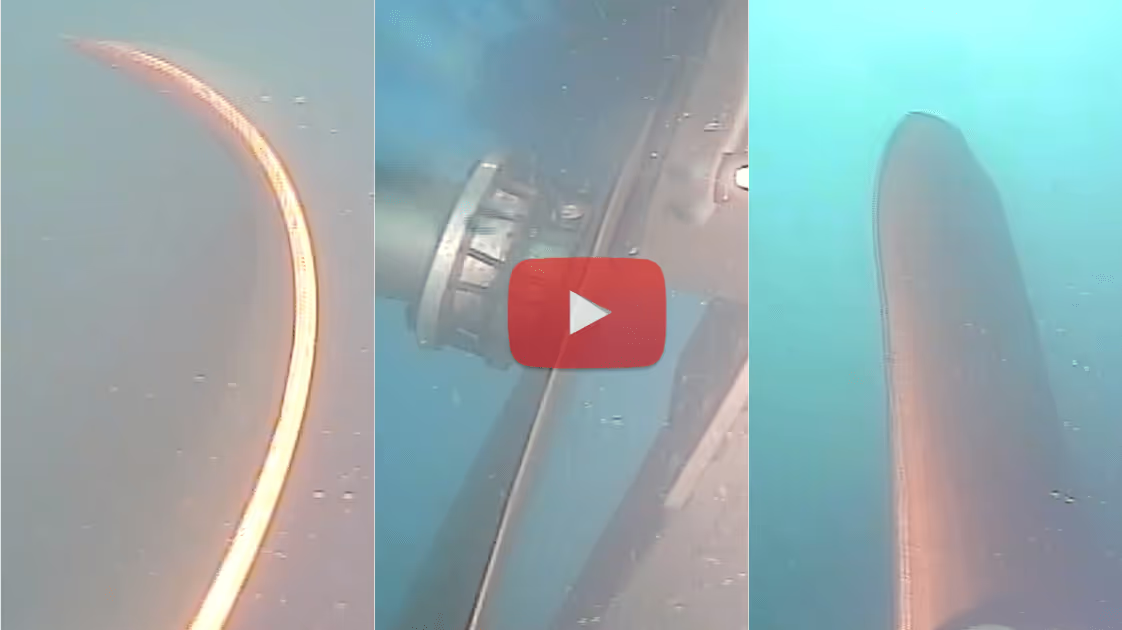
Problem
An Subsea Global Solutions partner agency in China contacted us with an urgent enquiry to perform an underwater inspection on a vessel that had experienced contact damage to its propeller while underway to an anchorage in Busan, Korea. The client indicated that they were experiencing severe engine loading and excessive vibration, so we prepared for various repair options to execute upon completion of the underwater inspection, including underwater propeller blade straightening and underwater propeller blade cropping and balancing. The initial underwater inspection revealed large aft-ward deflections up to 100 degrees on all four propeller blade trailing edge tips. Having a global presence Subsea Global Solutions responded with in an hour and provided the repair options to the client with cold static load propeller blade straightening as our recommended procedure. The client was reluctant to proceed at first, as they had received competing quotes from alternate commercial diving companies which were more economical. It was understood that this was because the procedures proposed by the alternative commercial diving companies included methods such as underwater propeller blade cropping. We wanted to avoid cropping, since all four propeller blades were ideal candidates for restoration to near OEM design geometry without cropping. After further enlightening our client on the distinct differences, vessel performance affects, and outlining the benefits of underwater propeller blade straightening versus propeller blade cropping (as referenced in the Subsea Global Solutions Case Study - Underwater Propeller Blade Straightening: Cold Static Loading), the client decided to go with the Subsea Global Solutions underwater propeller blade straightening procedure.
Solution
Our Subsea Global Solutions Busan team mobilized 3 experienced commercial diver technicians, 2 in-house trained commercial diver propeller technicians, and the virtual support of a Senior Level 3 Propeller Technician from our Vancouver office who could not travel to the job site due to COVID-19 travel restrictions. Subsea Global Solutions Vancouver is the proud home of our expert Propeller Technician instructors who work hard to educate and train our 165+ full-time commercial diver technicians through the Subsea Global Solutions Maritime Academy. Subsea Global Solutions continues to adapt to the ongoing COVID-19 crisis by serving our clients and repairing immobilized vessels in whatever ways possible. We want to help the world trade activity to continue and to protect the well-being of our valued seafarers (Announcement: Subsea Global Solutions Becomes A Signatory to the Neptune Declaration).
We began the underwater repair process with a close visual inspection for any linear surface defects in the deflected section tension sides (suction faces)—none were sighted. We then documented the current geometry of each blade to scale on the design drawings identifying the key locations to position our underwater propeller blade press while considering section thickness, fold lines, deflection angle radii, and the correct target geometry for propeller blade restoration. We started with the 12 o’clock blade and as each blade was completed the vessel crew jacked the turning gear to place the succeeding blade to the 12 o’clock position. After completing each propeller blade’s underwater straightening process, a subsequent close visual inspection was performed to ensure that no micro fractures or other linear defects had developed during the straightening process—again, none were sighted.
Conclusion
With a 12-hour repair window, all four blades were successfully restored to near design geometry and as per iACS Rules (ABS Reference: Rules for Survey After Construction, Part 7, Section 10 – 1.9.2 (b))—“NiAI Bronze propellers do not require stress relieving treatments after straightening”. The propeller was considered safe for continual use without operational restrictions until the vessel’s next scheduled dry docking, to which Subsea Global Solutions would recommend a detailed inspection supported by dye penetrant to ensure the propeller is free of latent defects. Upon departure from Busan, the client reported a successful sea trial with all engine parameters and vessel performance restored to pre-damage values. The project was completed in a safe, professional, and efficient manner without removing any material from the propeller blades.
Our goal is to always deliver unrivaled service. From hull maintenance to complex ship repair, there is only one global resource you can truly rely on; Subsea Global Solutions.