
Case Study
Subsea Global Solutions Completes an Afloat Rudder Stock Seal Replacement
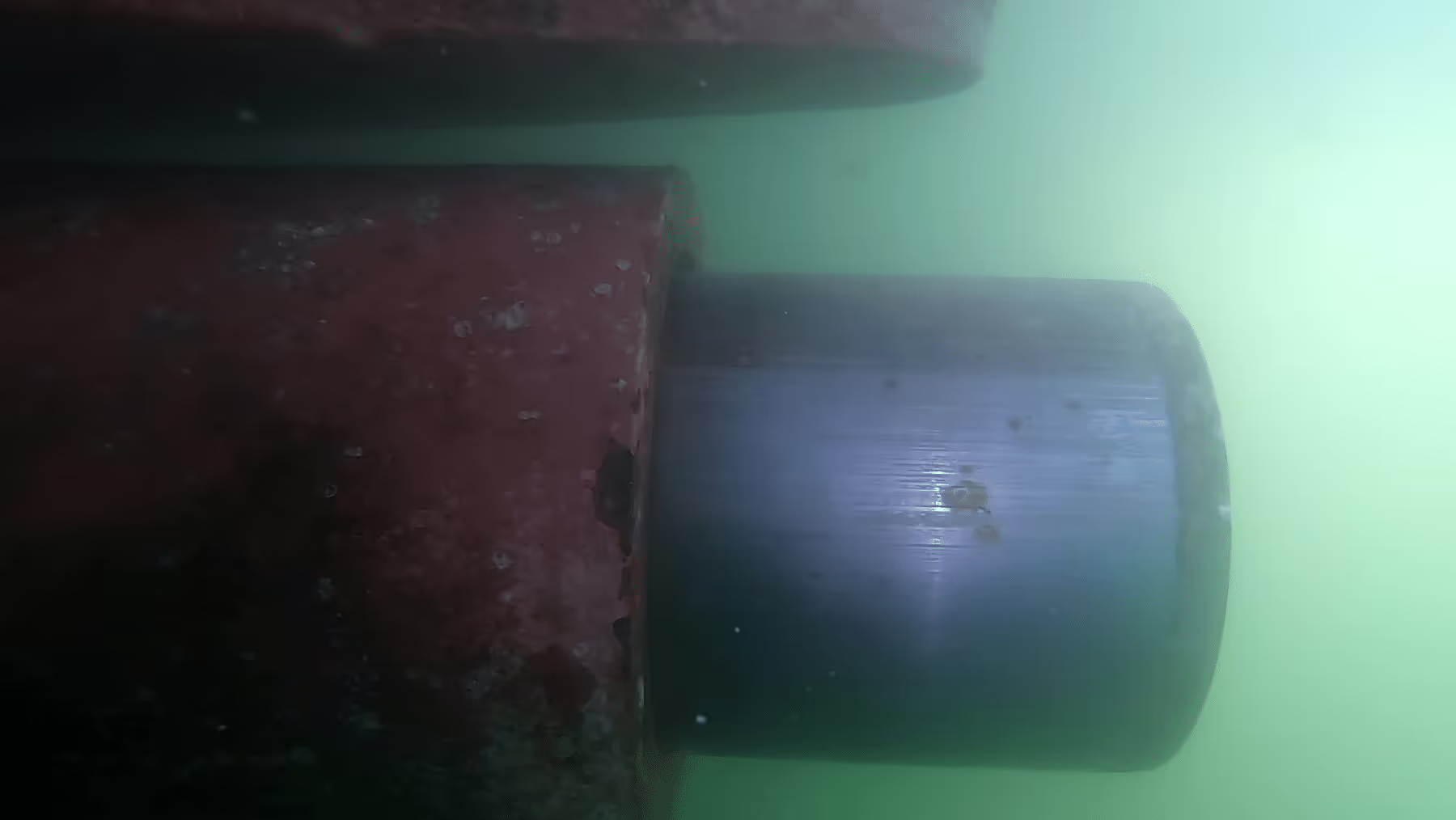
Problem
A client contacted Subsea Global Solutions requiring underwater support to replace a leaking rudder stock seal on the port side rudder during the vessel’s layup at a shipyard in Corpus Christi, Texas. The client had first contacted the shipyard for support on this project, but the shipyard was not prepared to take the responsibility for lowering the rudder while the vessel was still afloat. Subsea Global Solutions, having years of experience with complex underwater repair projects such as this, was willing to take on the challenge with confidence for both segments of the work—internally and externally.
Solution
The Subsea Global Solutions centralized Technical Repair Department worked closely with the rudder OEM, vessel owners, and Class to develop a unique rudder repair procedure eliminating the need of cutting open the deck plate for the steering actuator removal and included both the underwater and internal works. Once the repair procedure was approved, we were ready complete the works in 5 x 14-hour shifts with 6 commercial diver technicians and one project manager from Houston, Long Beach, and Port Angeles. The vessel superintendent was not able to be present on the job site due to COVID-19 travel restrictions, so Subsea Global Solutions filled this void by handling the project logistics and responsibilities with the attending Class Surveyor.
The project was coordinated with two Subsea Global Solutions teams—an external dive team and an internal technical team. The dive team began by disengaging the rudder flap slide bar and establishing 15-ton rigging points using underwater welding procedures in accordance with the Class A requirements of AWS D3.6M: Underwater Welding Code for both the overhead (4F) and the vertical (3F) positions. In parallel, the internal team was working to remove the rudder feedback cables and preparing the rudder stock for removal. Our repair procedure required the rudder stock to be released from the steering actuator and lowered enough to allow the new seals to be slipped over the rudder stock, since these particular seals were not the bondable type as with other seal related projects Ssubsea Global Solutions performs. The internal team’s next steps were to dismantle the seal housing, remove the damaged lip rings, and then secure the seal housing so it would not get damaged when the rudder stock was lowered by the dive team. The dive team completed the rigging point installations and successfully load tested them to ensure they would hold the full weight of the rudder blade and rudder stock, which was about 40 tons. With the chain hoist now securely in place on the rudder, the internal team removed the rudder stock nut and installed high pressure pumps to pressurize the taper while closely following the OEM procedure. The rudder stock was pressurized until it released from the steering actuator and the load was transferred to the underwater chain hoist. At this point, the dive team had full control of the load and began to lower the rudder blade and rudder stock until there was enough clearance over the top of the rudder shaft to install the new seals and O-rings. Once the new seals and O-rings were secure on the rudder stock, the dive team began to raise the rudder back into position in the same controlled method receiving precise direction from the internal team until the rudder stock was seated correctly into the steering actuator rotor. Once seated, the internal team followed the OEM procedure to reinstall the rudder stock nut and pressurize the taper to hydraulically push the rudder stock back to the original push up marks while in the presence of the attending Class Surveyor. After completing the push up and securing the rudder stock nut was completed, the internal team was able to safely reinstall the new seal package and housing back into the deck flange. The new seals where properly greased and each received a feeler gauge test to ensure proper clearance was met. After successfully completing the seal installation to the satisfaction of attending class surveyor, both Subsea Global Solutions teams began reinstalling each related component then de-rigging the chain hoist, removing the rigging points from the hull and rudder, and installing corrosion protective barriers over the bare metal locations of the hull. Finally, the vessel crew performed a successful rudder test to confirm the “zero” on the bridge’s controls matched rudder actuator position and the centerline on rudder blade underwater.
Conclusion
This complex underwater repair was completed to the client's satisfaction in 5 days in conjunction with various other repair works. Subsea Global Solutions managed both the underwater and internal portions of this repair to ensure each phase was executed seamlessly. Having a centralized Technical Repair Department does make a difference when managing complex underwater repairs on a global scale, as it allows Subsea Global Solutions to ensure both our Clients and Class receive the same familiar experience from Subsea Global Solutions they are used to, regardless of where the project is taking place.
Our goal is to always deliver unrivaled service. From hull maintenance to complex ship repair, there is only one global resource you can truly rely on; Subsea Global Solutions.