Hull Cleaning ROV
Ship Hull Cleaning ROV for Expands Vessel Cleaning Options
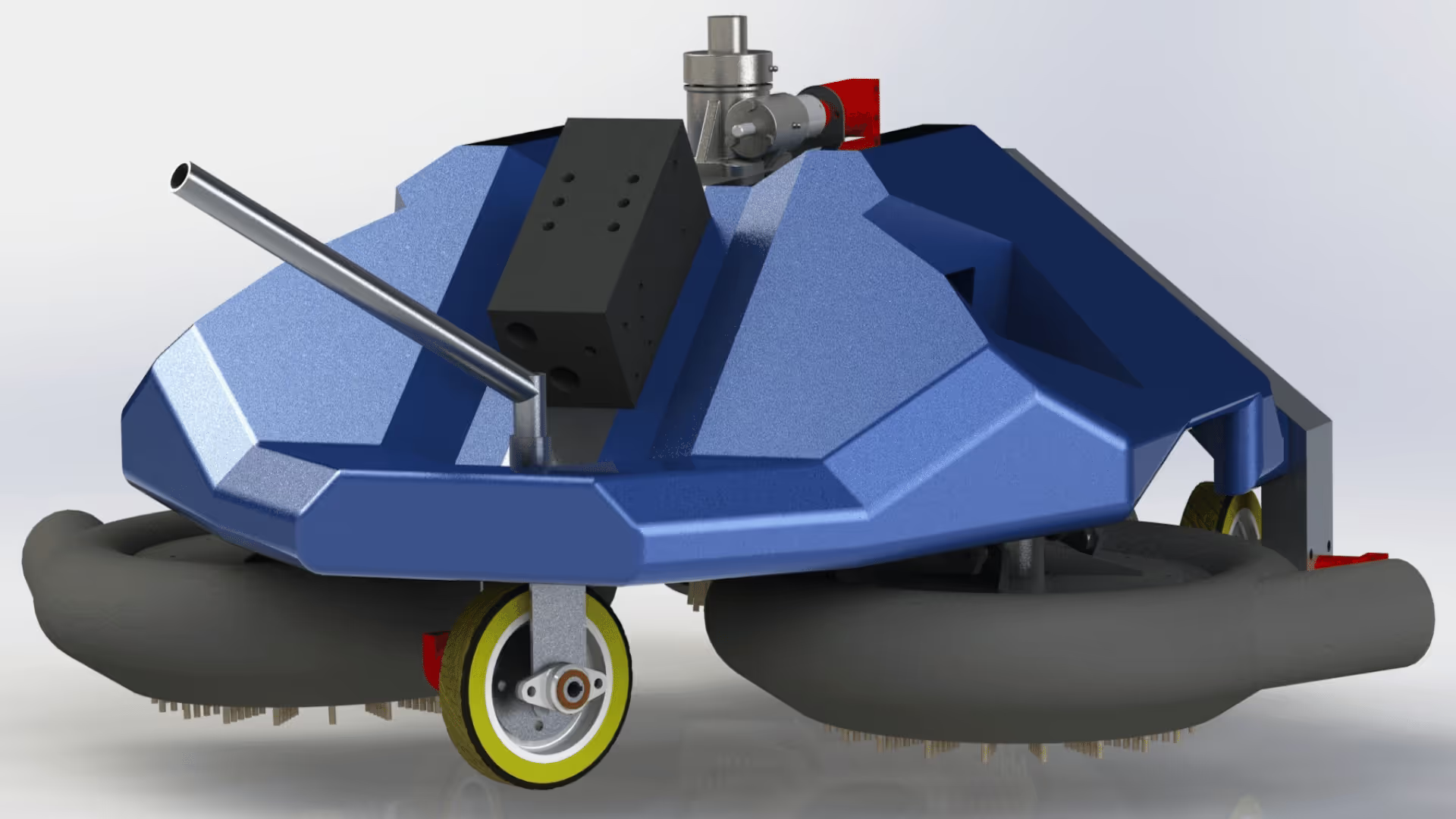
.truncate { white-space: nowrap; text-overflow: ellipsis; }
Our new ROV vessel hull cleaning system works great with:
Cleaning with our ROV can be fully filtered with a 3-stage filtering process reducing the effluent to less than 1 micron with clean water returned to the sea. It can also be deployed offshore with no filtering.
Remotely Operated Vehicle (C-ROV) has been approved in several locations with more coming soon. It is now available for cleaning in these ports, and anywhere environmental issues permit cleaning:
Learn how Subsea Global Solutions performs underwater hull cleaning with a ROV.
A major marine contractor required expert diving support for the installation of a structural cap at a floating drydock mooring facility located within a restricted-access naval base in San Diego. The operation involved precision underwater cutting, structural steelwork placement, and integration with concrete construction, all under tight schedule and engineering constraints.
View Full Case StudySubsea Global's Ops Manager Herschel Smith and Dive Supervisor Shawn Henly will be at the Pacific Marine Expo Nov 20-22.
View Full Case StudyClass approved shell plate underwater damage repairs to offshore semi-submersible platform without drydocking.
View Full Case StudyDiscover how Subsea Global Solutions expertly repaired a corrosion hole in an offshore supply vessel’s bilge tank. Our Trinidad team delivered a class-approved shell plate replacement, restoring the 90-meter vessel to full operational readiness with minimal downtime.
View Full Case StudyIn October, Subsea Global Solutions held its advanced underwater welding training course in our training center in Long Beach, providing a comprehensive 10-day program designed to hone practical skills and qualify participants for new joint geometries and/or new welding positions.
View Full Case StudyUnderwater welding, especially underwater wet welding, is gaining more and more acceptance. This article from Welding & Cutting Magazine takes a deep dive into types, procedures, and codes.
View Full Case StudySubsea Global Solutions was tasked with completing a routine propeller polishing and hull inspection for a commercial vessel docked at the Port of Palm Beach. This service, part of the vessel’s ongoing maintenance schedule, ensured optimal performance and efficiency.
View Full Case StudyA big thank you to Captain Kate for sharing a behind-the-scenes look at Subsea Global Solutions in action on a propeller polishing project.
View Full Case StudyBy utilizing a multi-stage polishing process and diver / technicians trained in the proper analysis of the propeller condition, Subsea Global Solutions' process has proven to be an integral part of fuel efficiency programs. The benefits of maintaining a polished propeller have been known for years, but what has not been known is "how smooth is smooth"?
View Full Case StudyWhen a vessel experienced a significant shaft seal leak, Subsea Global Solutions mobilized rapidly to perform a full seal replacement—without a dry dock or habitat—ensuring minimal downtime and maximum efficiency.
View Full Case StudySubsea Global Solutions was called upon to perform a critical underwater stern seal exchange on a tanker docked in Curacao. Facing significant oil leakage, the client urgently needed a trusted partner with the expertise and resources to complete the repair efficiently, safely, and without disrupting the vessel's schedule.
View Full Case StudyThe client indicated that the tailshaft had shifted aft approximately 200 mm when the ship’s crew was doing maintenance on the shaft coupling. It resulted in the aft water seal losing contact with the liner, causing large amounts of water ingress into the stern tube.
View Full Case StudyDiscover how Subsea Global Solutions expertly repaired a corrosion hole in an offshore supply vessel’s bilge tank. Our Trinidad team delivered a class-approved shell plate replacement, restoring the 90-meter vessel to full operational readiness with minimal downtime.
View Full Case StudyIn October, Subsea Global Solutions held its advanced underwater welding training course in our training center in Long Beach, providing a comprehensive 10-day program designed to hone practical skills and qualify participants for new joint geometries and/or new welding positions.
View Full Case StudyUnderwater welding, especially underwater wet welding, is gaining more and more acceptance. This article from Welding & Cutting Magazine takes a deep dive into types, procedures, and codes.
View Full Case StudyWhen a propeller sustains damage beyond the straightening capabilities of even the largest press equipment, hydrodynamic corrections offer an innovative and effective solution.
View Full Case StudyNot all propeller damage can be straightened. When blades are fractured, chipped, or excessively bent, cropping becomes necessary. However, cropping an odd-numbered blade propeller presents unique challenges that must be carefully managed.
View Full Case StudySubsea Global Solutions’ proprietary propeller straightening technology offers a far more efficient and cost-effective alternative to blade cropping.
View Full Case StudySubsea Global Solutions completed a critical in-water steering seal repair on a cable vessel in San Diego. Our team rapidly designed, fabricated, and installed a custom packing gland housing, ensuring minimal downtime and keeping the vessel on schedule.
View Full Case StudyWhen a vessel experienced a significant shaft seal leak, Subsea Global Solutions mobilized rapidly to perform a full seal replacement—without a dry dock or habitat—ensuring minimal downtime and maximum efficiency.
View Full Case StudySubsea Global Solutions was called upon to perform a critical underwater stern seal exchange on a tanker docked in Curacao. Facing significant oil leakage, the client urgently needed a trusted partner with the expertise and resources to complete the repair efficiently, safely, and without disrupting the vessel's schedule.
View Full Case StudyThe client indicated that the tailshaft had shifted aft approximately 200 mm when the ship’s crew was doing maintenance on the shaft coupling. It resulted in the aft water seal losing contact with the liner, causing large amounts of water ingress into the stern tube.
View Full Case StudyThe installation of complete SOx scrubber systems is entirely possible without taking the vessel out of the water. Subsea Global Solutions' involvement is focused on precision cutting of the hull penetrations for the sea chest openings and overboard spool pipe installation below the waterline.
View Full Case StudyThe client was in need of a turn-key—class approved—permanent repair. This included a single contractor that would manage the internal technical repair team, commercial diver team, prefabrication of the new spool pieces with flanges, final application of the 5-year warranty POLYFLAKE protective coating to 3000 microns on the new spool pipes, and achieving final class approval for the full repair procedure.
View Full Case StudyIn 2024, Subsea Global Solutions completed a complex overhaul of eight thrusters on the La Muralla oil rig, led by our Curaçao-based team, ensuring the rig's peak performance through rapid, on-site servicing.
View Full Case StudyThe benefits of removing a damaged bow thruster afloat are many. The customer was able to prevent further damage to the bearings and gears caused by the presence of seawater in the gear housing and the procedures allows the units to be overhauled prior to the vessels next dry-dock—or, they can be re-installed afloat by Subsea Global Solutions, which would help to eliminate the need for additional tug cost.
View Full Case StudyThe project was executed with two Subsea Global Solutions teams working around the clock. While the vessel trimming process was in motion, the team onboard the vessel began to drain the oil from the thruster while the dive team began removing the bow thruster tunnel gratings to gain full access to the bow thruster.
View Full Case StudyA major marine contractor required expert diving support for the installation of a structural cap at a floating drydock mooring facility located within a restricted-access naval base in San Diego. The operation involved precision underwater cutting, structural steelwork placement, and integration with concrete construction, all under tight schedule and engineering constraints.
View Full Case StudySubsea Global's Ops Manager Herschel Smith and Dive Supervisor Shawn Henly will be at the Pacific Marine Expo Nov 20-22.
View Full Case StudyClass approved shell plate underwater damage repairs to offshore semi-submersible platform without drydocking.
View Full Case StudySubsea Global Solutions is proud to announce that the authorities in Singapore have granted approval of our advanced hull cleaning services for vessels, allowing underwater cleaning to take place while vessels are engaged in cargo work at the terminal.
View Full Case StudySubsea Global Solution's impressive biofouling cleaning operation on a massive FLNG vessel in Busan. Explore the difficulties and creative approaches.
View Full Case StudyA wide range of brushes and scrapers are available to tailor your hull cleaning to the amount of fouling, how aggressive you want to be, and the environmental considerations. We work with you to achieve exactly the job you want.
When you have any special circumstances, yet still need a professional hull cleaning, call Subsea. Our new ROV vessel cleaning system is ready to deploy.