Technical Situation
A floating production storage and offloading (FPSO) unit is a vessel used for the production, processing and storage of oil and gas.
A Blue-Chip oil & gas company incurred several defects and cracks in a critical attachment member of an FPSO’s hull – these defects required repair to allow continued operation.
As FPSOs are cyclically loaded and unloaded and experience rough conditions at sea, this type of hull defect tends to worsen as time passes.
FPSOs are often conversions from old tanker ships which do not have double hull structures.
To ensure continued safe operation and remain in compliance with regulatory requirements, this type of defect must be permanently repaired.
Business Situation
There is no industry accepted solution to fix a FPSO defect of this type.
The client was contemplating to disconnect the vessel from the location (250+ miles offshore) – this is extremely expensive, and could require the client to abandon the well and/or lose rights to the location entirely.
The Subsea Global Solution
Subsea’s underwater wet welding technology allows the vessel to continue to produce oil while being permanently repaired.
Brazilian local content regulations require the use of local divers – Subsea provides technology licensing, training, supervision and project management .
While offshore oil & gas clients were initially skeptical to the Subsea approach, the Company has achieved recognition of this permanent repair process which is generating more inquiries for long-term repair projects utilizing its superior technology.
The Company’s current contract for this case study project was signed in 2016 and expires in 2021 – its success is well documented in the space.
CONTACT US
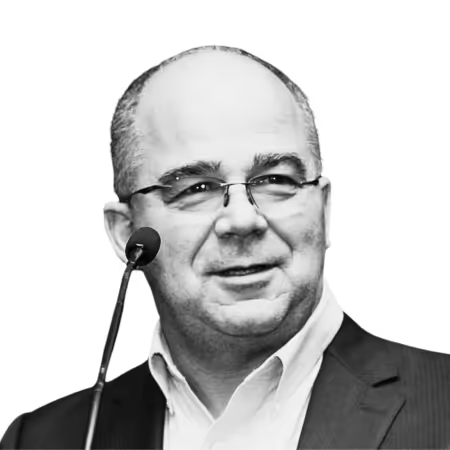
Uwe Aschemeier
Uwe Aschemeier is a German born and educated Welding Engineer who has evolved through the metals industry by studying mechanical engineering and welding engineering at various advanced education institutions in Germany. Mr. Aschemeier worked for the German Welding Society at its Institute in Munich for several years prior to moving to the United States of America. He has continued his expertise development by working for the Chicago Manufacturing Center, a non-profit consulting organization as well as Charcas Engineering/Domson Engineering in Toronto, Canada. In 2000, he joined H.C. Nutting Company in Cincinnati, where he worked as a senior welding engineer, commercial diver, and consultant. After consulting for Miami Diver for several years in welding related topics, he join Miami Diver LLC. (now Subsea Global Solutions) as their senior welding engineer and commercial diver in 2007. Over the next 10 years Mr. Aschemeier led the development of wet welding procedures to the level of A class through a JIP (joint industrial project) with DNV/GL and the GL testing lab in Hamburg to achieve for the first time A class groove weld procedures. This was done by showing on a consistent basis wet welding that meets A class standards, enabling true structure repairs that can be done on vessels with wet welding procedures. Mr. Aschemeier serves on the ISO/TC 44/SC 15 - Underwater welding committee representing the USA in this EU wet welding standard. He is the vice chair on D3.6M underwater welding standard, and also sits on 3 welding committees for AWS Standards and task groups as chair or vice chair. He has authored and co-authored numerous welding and NDE related articles published in the “Welding Journal”, “Inspection Trends” and other national and international trade magazines. He also serves in the “Fachausschuss Unterwassertechnik” (Technical committee underwater technology) from the German Welding Society (DVS). For six years, he served on the AWS Board of Directors.