Underwater Welding & Repairs
Wet Underwater Welding
Permanent CLASS APPROVED underwater welding & repairs were thought to be IMPOSSIBLE until Subsea Global Solutions pioneered the wet underwater welding process. Class approved permanent repair processes are established using underwater wet welding, atmospheric dry welding or hyperbaric dry welding for permanent repairs to incidental hull damage below the water line. With an in-house Engineering department headed by our Senior Welding Engineer, who has decades of welding experience on topside and underwater, Subsea Global Solutions is capable of Structural Engineering and writing repair procedures detailing the welding process and scope of repair to be developed upfront for pre-approval by Head Offices of major Classification Societies or insurance underwriters. Having a pre-approved repair procedure by the Class damage department gives the customer a guarantee that a permanent repair is achieved on time wherever or whenever required.
Welder/Diver technicians are trained, qualified and their qualifications renewed every 2 years in one of the three training tanks at Subsea Global Solutions facilities. All welders WPQR’s are done on Classification Society certified paper to the requirements of Class "A" as outlined in AWS D3.6M- - Underwater Welding Code.
Subsea Global Solutions
is the only diving company globally to have a Workshop Approval for Underwater Welding by DNV- GL.
Subsea Global Solutions designs and manufactures cofferdams of all sizes and configurations. Well versed in the development of flexible as well as rigid hyperbaric (open bottom) or atmospheric cofferdams.
Hydroweld Representatives and America's Hydroweld Training Center
Hydroweld FS wet underwater welding electrodes are the result of significant research and development into flux formulations, filler metals and supplementary coatings. They are designed to work in all positions in fresh water, brine or saltwater, and have been used to successfully perform wet weld repairs have been performed to a depth of 300 meters. Their outstanding user-friendly properties and wet welding characteristics, easily produce high quality wet welds to internationally recognized standards. Hydroweld FS is the electrode of choice where high-quality wet welding is required. They have meet the class A requirements of AWS D3.6M for fillet and groove wet welds as has been witnessed by Lloyds Register of Shipping (LR), American Bureau of Shipping (ABS), Det Norske Veritas (DNV), Bureau Veritas (BV), Rina and Germanisher Lloyd (GL). Hydroweld FS wet welding electrodes are currently the only wet underwater welding electrodes approved for permanent and temporary repairs on war ships by the British Ministry of Defense (MoD). This was gained after intensive underwater comparability testing and further NDE and destructive testing against all other commercially available wet welding electrodes by the MoD and The Welding Institute (TWI). As a result, the electrodes are now included in the NATO codification system.
To learn more about underwater welding at SubSea Global Solutions, check out our Underwater Welding case study here. here.
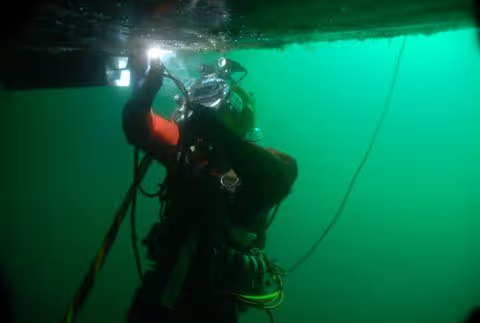
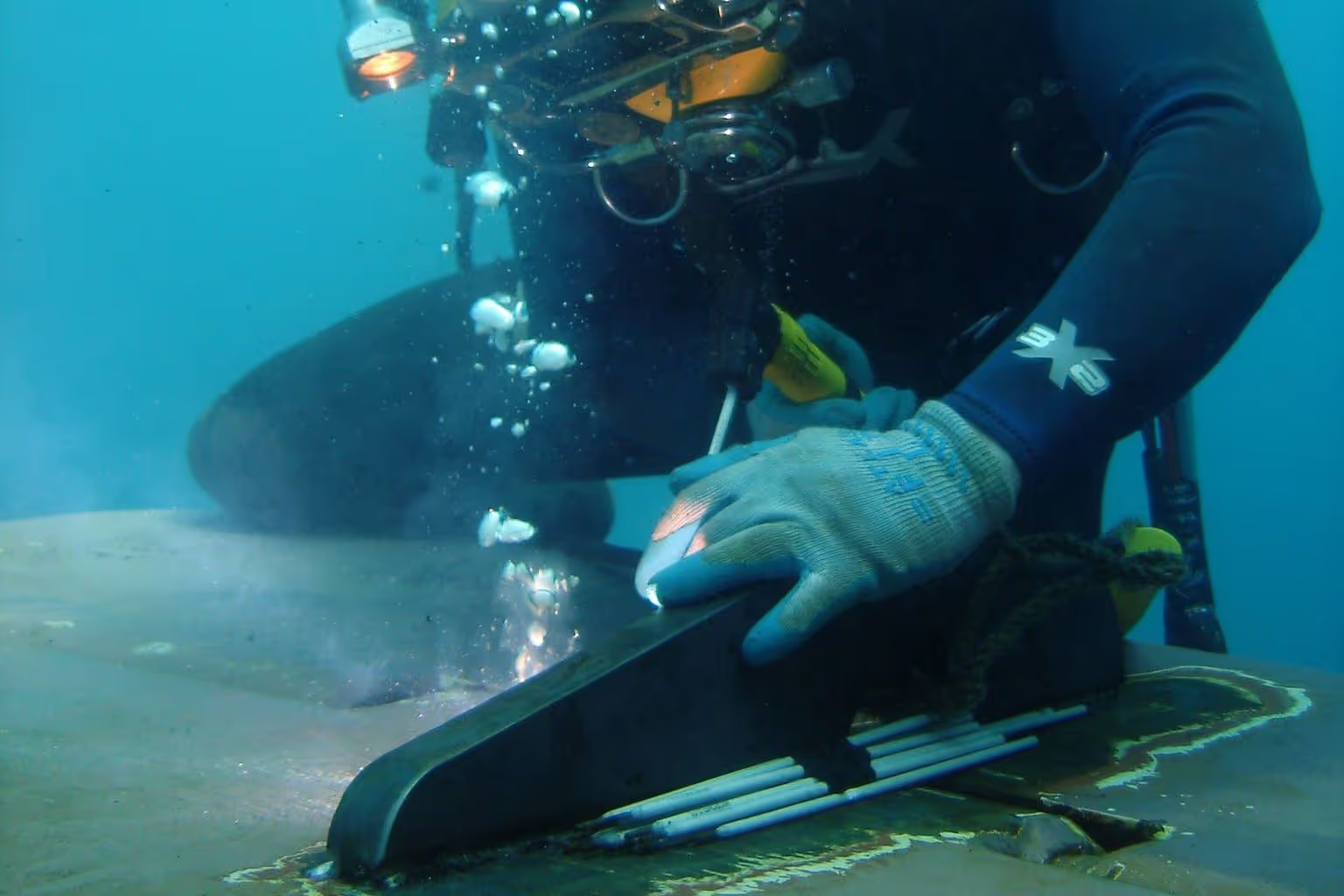
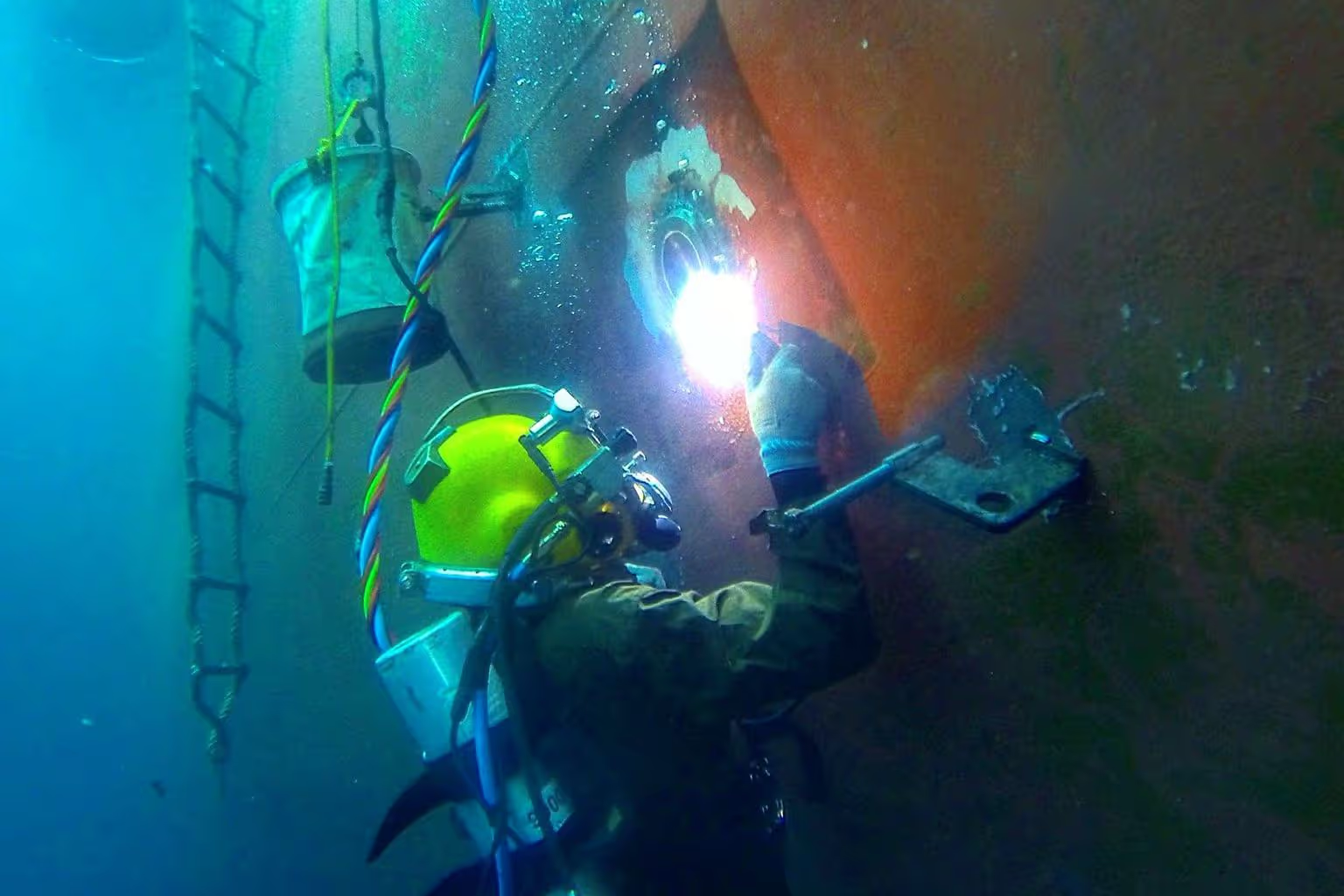
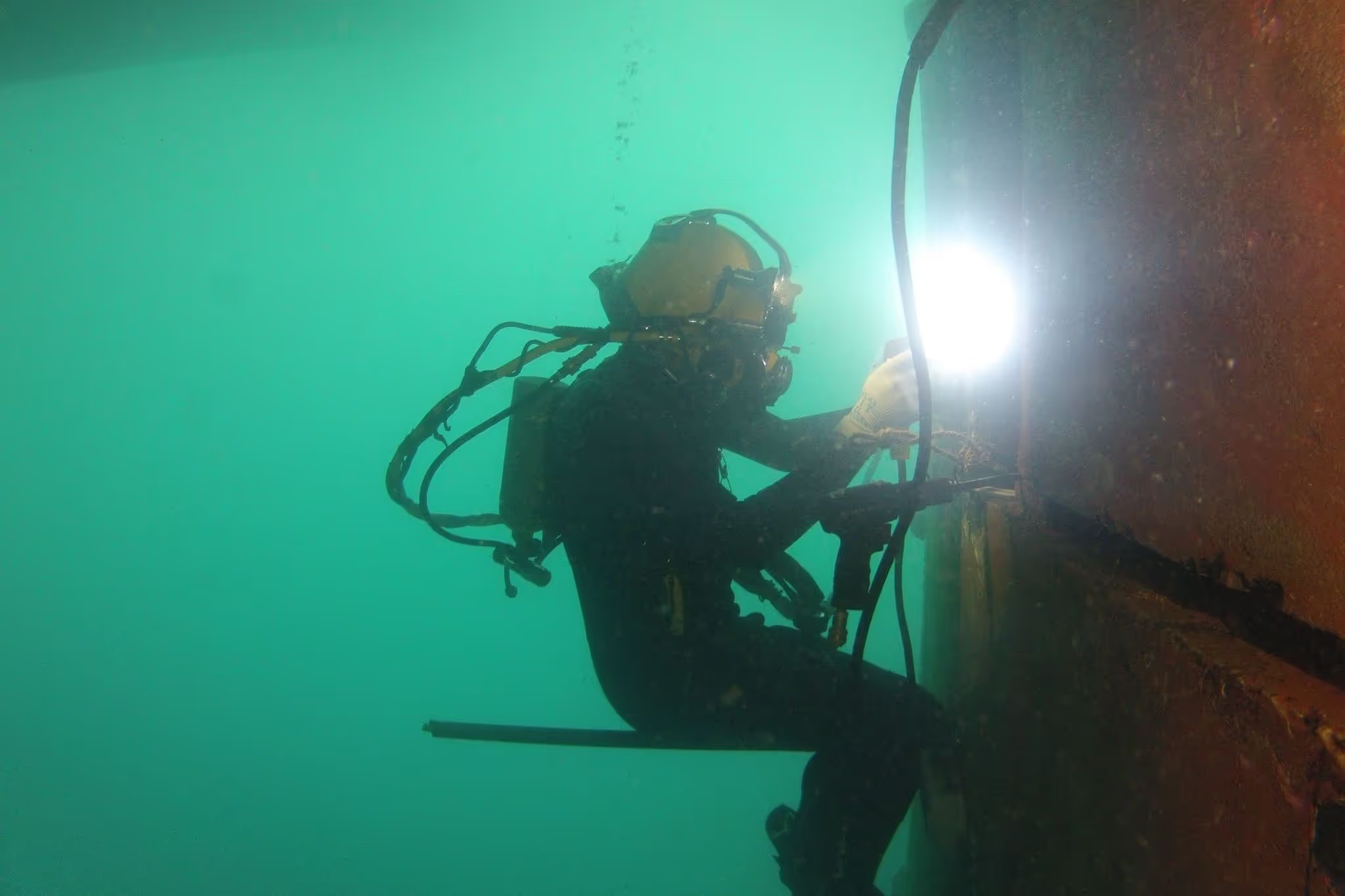
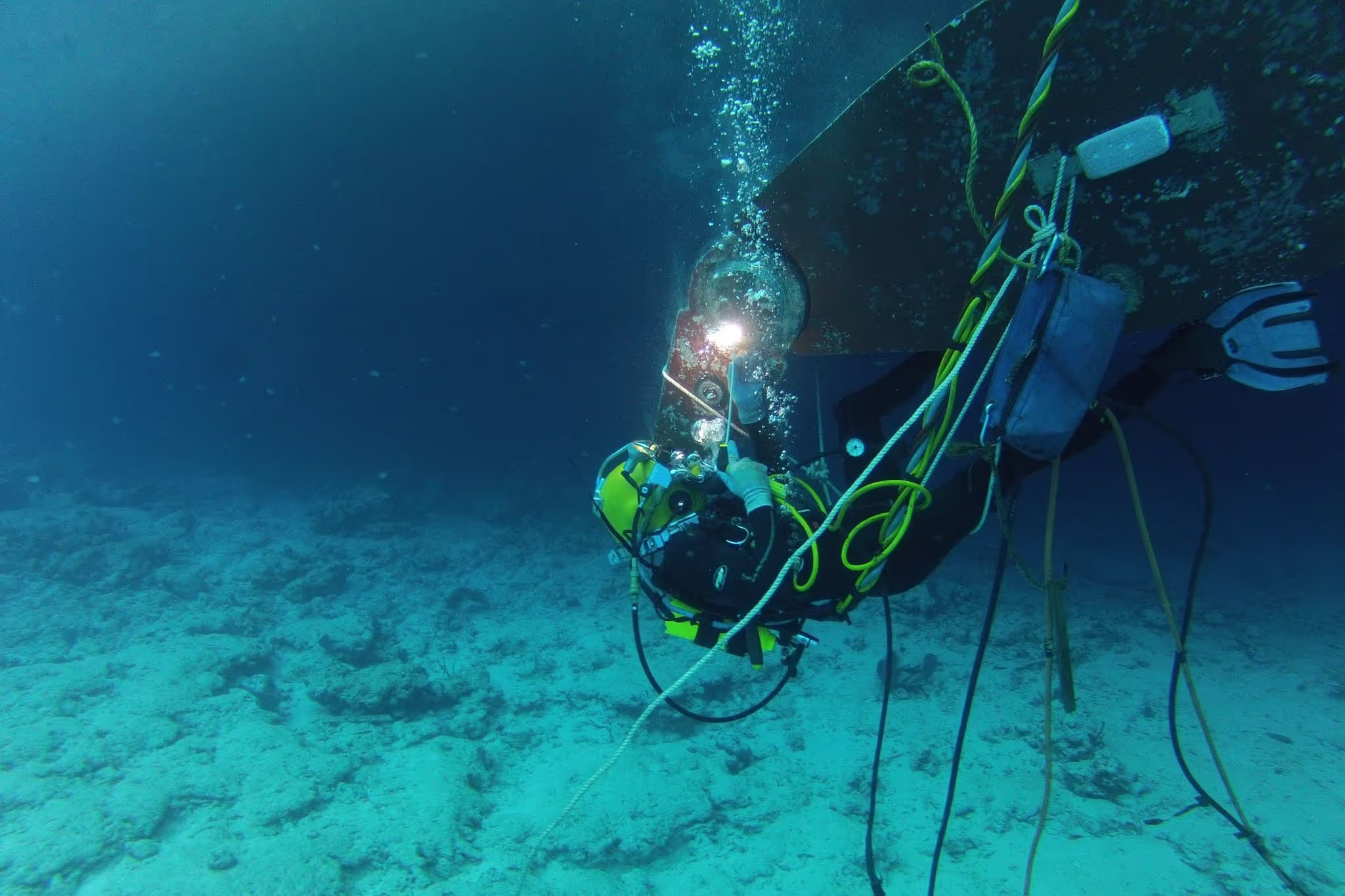
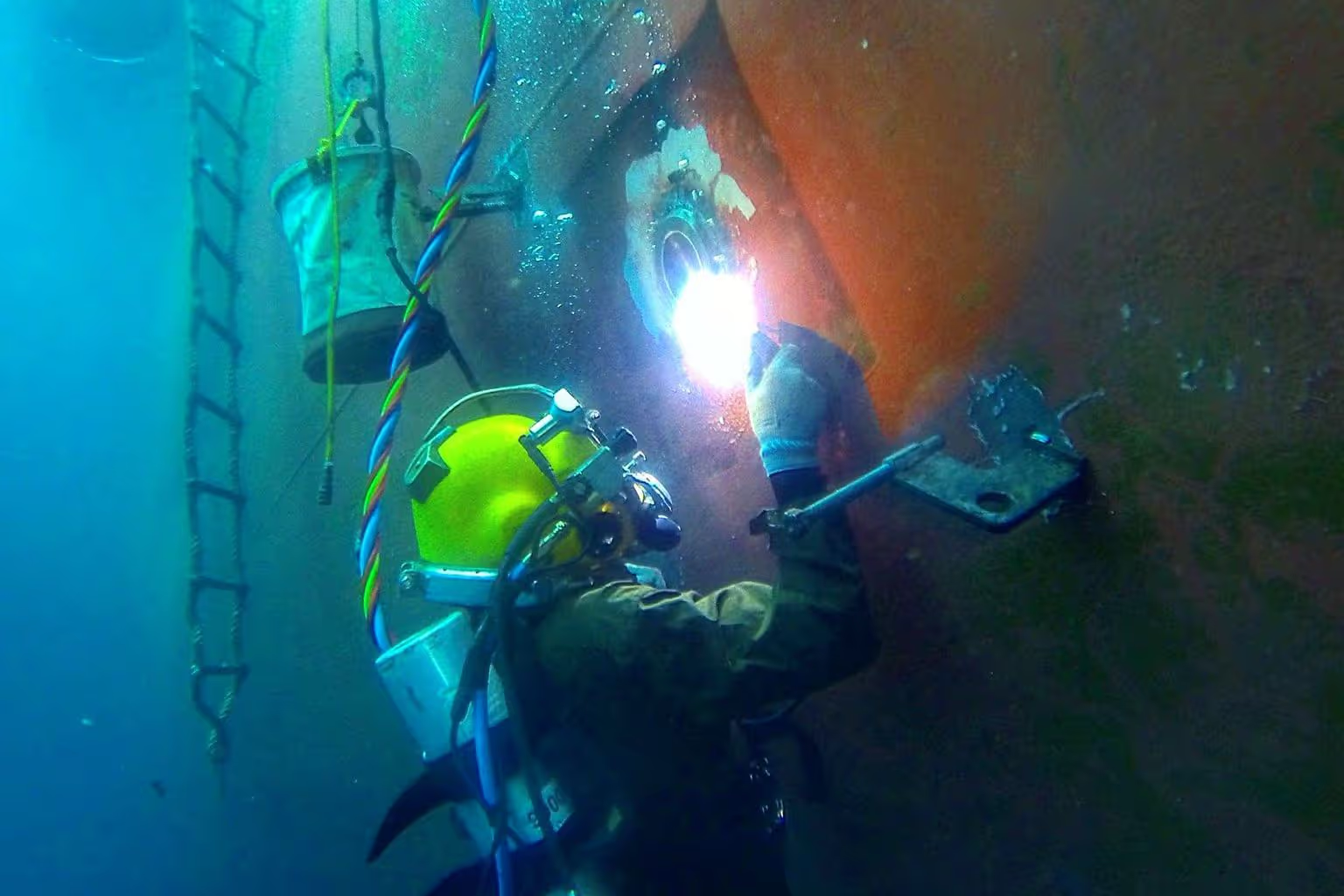
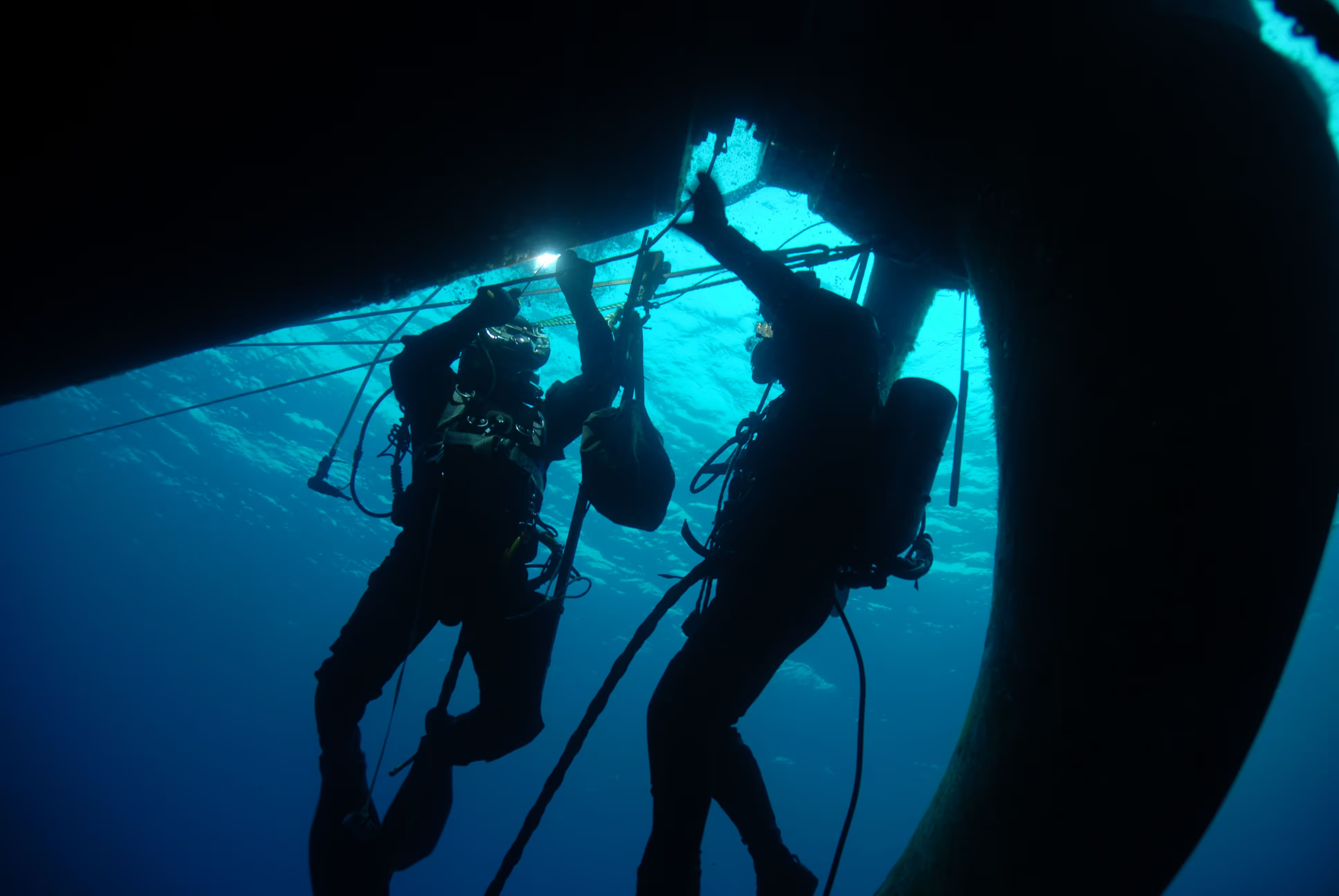