
Case Study
Offshore installation, underwater shell plate damage, class approved repair without drydocking
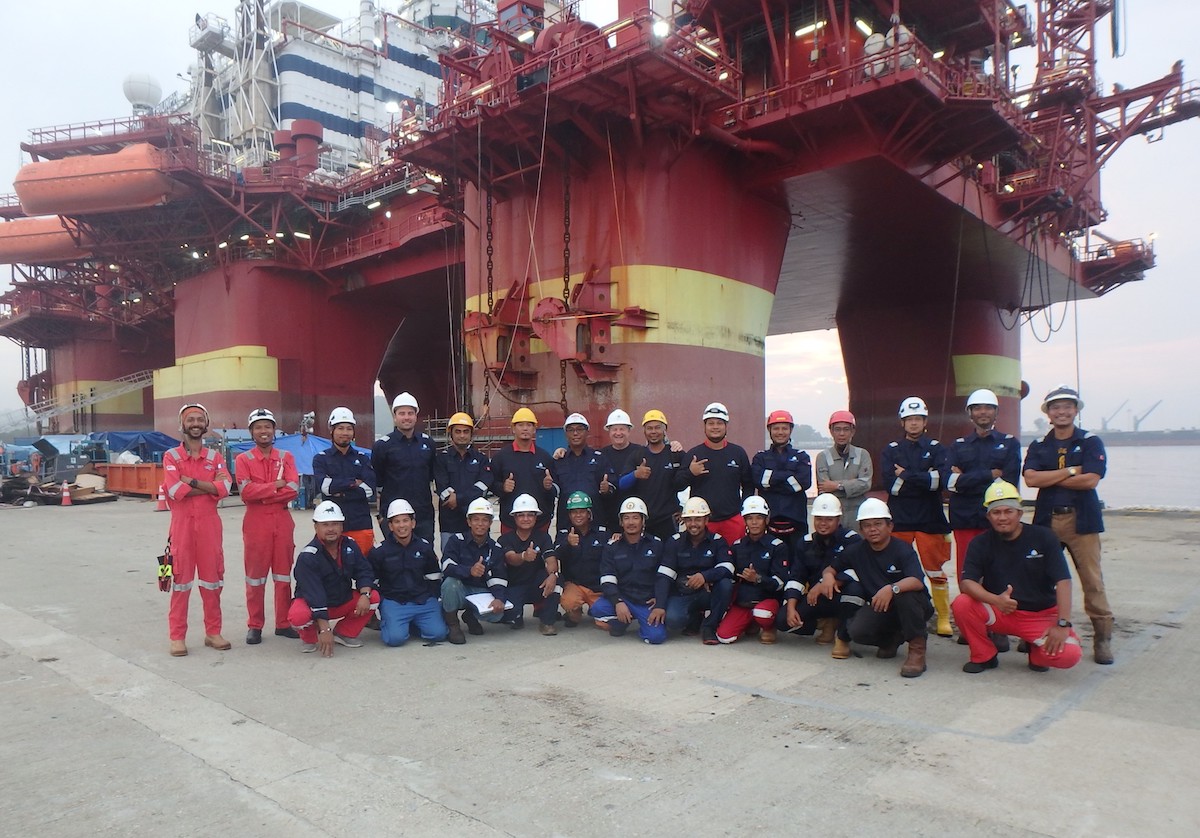
Subsea Global Solutions supports offshore asset maintenance with in-water technical repairs worldwide.
Subsea Global Solutions supports offshore asset maintenance with in-water technical repairs worldwide. So, an initial enquiry about a 27,000 GT semi-submersible accommodation barge with underwater hull damage asking to remove its thrusters to facilitate repairs, our experienced underwater specialists applied our ‘thinking in the water logic’ - what is the best and safest solution for you.
Normally this type of situation would require repositioning the unit to an available drydock of suitable capacity, and in this case demounting of the six large DP3 azimuth thruster systems to access the dock itself – all extra time and of course money for the owner operators.
Having successfully completed demountable thruster and underwater welding projects for offshore clients around the world, our Singapore project team was able to propose our alternative approach for the client to consider.
A dive team was promptly deployed, and their underwater inspection confirmed the extent of pontoon shell plate damage and took all necessary measurements to plan for a cofferdam to safely encompass the circa 6.5 by 3 meters of damaged shell plating. The project team explained the underwater procedures for the client/class approval of the plan and technical repair phases. Working with trusted local-content partners, Subsea Global Solutions provides win-win complete turn-key underwater solutions, providing savings for shipowners and can increase work capacity for shipyards who have suitable lay berths alongside while their drydocks are in use.
The substantial cofferdam, over 10 tonnes, was fabricated onsite and preparations made for the installation. Diver-technicians completed all the relevant underwater welding work in conformance with the Class A requirements of AWS D3.6 to be able to install the cofferdam safely. Once installed, and dewatered, fabricators and coded welders were then able to cut out and replace the damaged frames, stringers, and ultimately complete shell plate inserts, suitably keyed into the surrounding plating. Safe in the knowledge that the dive team was also monitoring the cofferdam installations. Meanwhile all quality control checks including vacuum and ultrasonic testing were completed to approval of the attending class surveyor.
In addition to the repair work, the unit’s future deployment required a full and thorough hull cleaning, including all the thrusters and niche areas to meet rigorous Australian biofouling inspection regulations, this work was completed concurrently, saving the client even more time.